Regulators
There are three basic types of scuba dive equipment, with open circuit being the most commonly used.
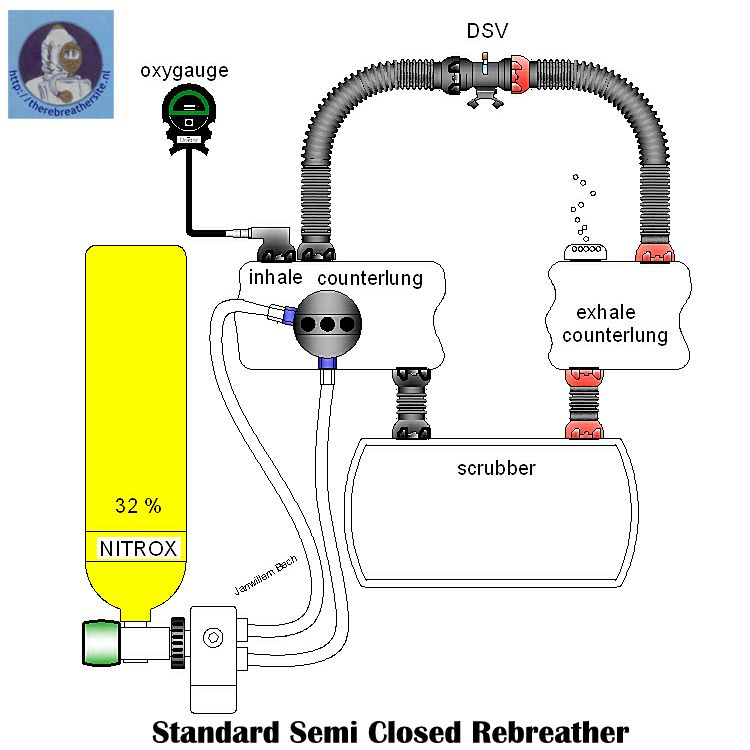
Semi-closed circuit: The diver inhales from a bag or counter-lung, and the exhaled breath cycles through a system that removes waste carbon dioxide and returns it to the counter-lung. It replaces consumed oxygen by employing a slow, steady flow of gas into the counterlung resulting in a slow, small stream of bubbles.
Semi-closed circuit equipment generally supplies one breathing gas such as air or nitrox or trimix. The gas is injected into the loop at a constant rate to replenish oxygen consumed from the loop by the diver. Excess gas must be constantly vented from the loop in small volumes to make space for fresh, oxygen-rich gas. As the oxygen in the vented gas cannot be separated from the inert gas, semi-closed circuit is wasteful of oxygen.
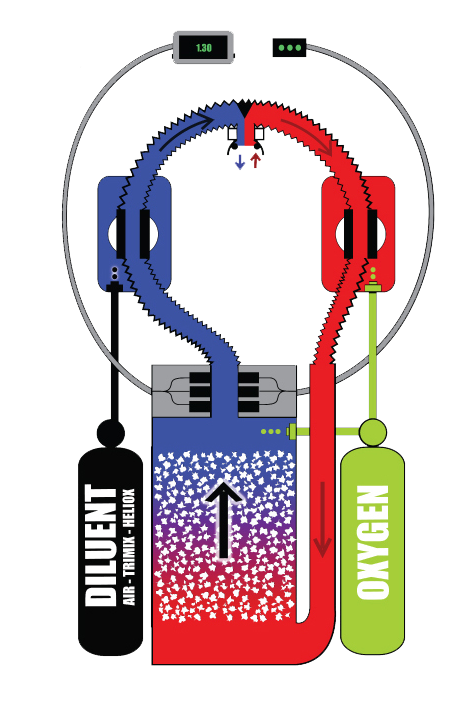
Closed Circuit
Closed-circuit: The inhaled breath comes from a bag/counter-lung, and when exhaled, is then cycled through a system that removes waste carbon dioxide and replaces the consumed oxygen, then returned to the bag. There are no bubbles.
Open-circuit: Most commonly used recreational diving regulators. When a diver inhales, they breathe in from a compressed gas cylinder. This is known as a demand system. When a diver exhales, the breath vents into the water and bubbles to the surface i.e. exhaled air is released directly into the water. It means that the path of the air from the cylinder terminates when it is exhaled into the water.
The open circuit consists of two stages, the 1st stage and the 2nd stage. To be able to breathe, air need to be delivered at a pressure that is about the same as the surrounding pressure. This is essentially what an open circuit scuba regulator does.
1st Stage: Has several ports that hoses attach to leading to the 2nd stages and other devices such as the pressure gauge, low pressure inflator and dry suit inflator. It basically functions as a pressure-reduction valve.
The primary function of the first-stage, is to take the high pressure air delivered from the tank and reduce it to an intermediate pressure.
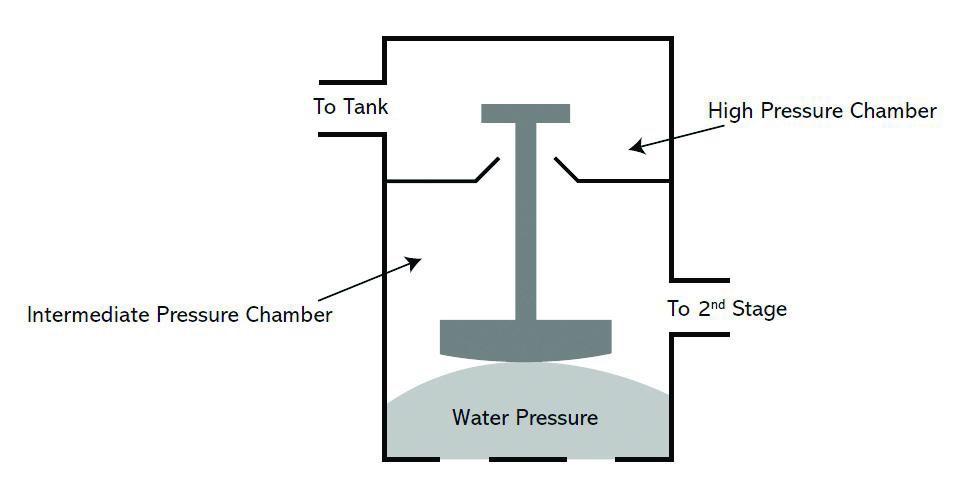
1st stage pressure sensing systems fall into two categories: piston and diaphragm.
In diaphragm first stages, the diaphragm is a flexible cover to the intermediate-pressure chamber. When the diver inhales, the pressure falls in the intermediate-pressure chamber below the desired ambient pressure and the diaphragm collapses inwards pushing against the valve lifter. This opens the valve letting high-pressure gas pass the valve seat into the intermediate-pressure chamber.
When the diver stops inhaling, the pressure in the intermediate-pressure chambers rises and upon reaching intermediate-pressure the diaphragm inflates outwards reducing the force on the valve lifter, letting the spring behind the valve close it i.e. the tank closes and air no longer flows.
Piston type first stages have a simpler design than the diaphragm type. With the piston-type first stage, the piston is rigid and acts directly on the seat of the valve. When the pressure in the intermediate pressure drops, as the diver inhales from the second stage, the piston lifts off the valve seat and slides towards the intermediate pressure chamber. This brings high pressure gas into the intermediate pressure chamber until the pressure in the chamber has risen enough to push the piston back onto the seat and close the valve.
2nd Stage: The second-stage continues the process discussed in above. It takes the intermediate pressure from the first stage and breaks it down to a pressure equal to the surrounding water pressure. The ambient pressure is sensed by a flexible second-stage diaphragm.2nd stages have two basic valve types, downstream and pilot valves.
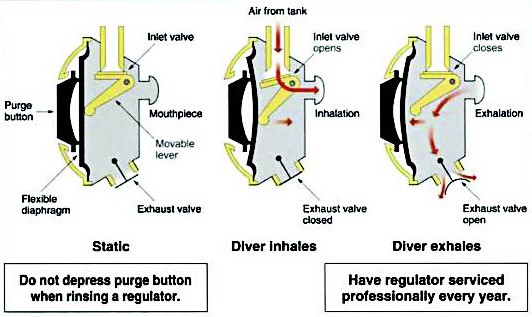
Downstream valves are the most common. When the diver inhales, the diaphragm pushes against a demand lever connected to a one way valve. This is because when inhaling, the pressure within the 2nd stage is lowered to below ambient water pressure and the water pressure presses in on the diaphragm. This causes the valve to open, supplying the diver with air. As the valve opens with airflow, it is called downstream (the pressure is trying to open the valve). **
When the diver exhales, the pressure in the 2nd stage exceeds ambient water pressure and pushes the diaphragm out allowing the lever to return to its normal position thereby closing the inlet valve. The increased pressure in the 2nd stage opens the exhaust valve allowing exhaled air to leave the 2nd stage.
One advantage with a downstream valve is that if the valve does fail, it almost always fails in the open position. This is called a fail-safe design (discussed more later).
** Contrary to downstream valves upstream valves open against the flow of air (the pressure is trying to close the valve).
With a pilot valve, when you inhale the diaphragm depresses on a lever on a small valve. The small valve releases air pressure (or creates a pressure imbalance) that in turn opens the larger main valve i.e. a smaller valve that opens a larger valve.
Drawbacks to pilot valves second stages include complexity and expense. They also tend to free flow easily, so most have dive/pre-dive switch. The pre-dive setting puts tension on the diaphragm so it doesn’t free flow as easily when it is not in the diver’s mouth.
Remember, pilot valves appear in the 2nd stage only!
Balanced and Unbalanced:
The difference between unbalanced and balanced regulators is to do with a design that offset variations in cylinder pressure.
In an unbalanced regulator/valve, the cylinder pressure presses on the valve and assists opening it. As the air in the cylinder is used up, the pressure lessens and therefore doesn’t assist with opening the valve. This causes a minor variation in performance. Cylinder pressure resists or assists the opening of valves in the first stage.
A balanced valve uses a design that routes high pressure cylinder air around both sides of the valve opening. This cancels out or balances cylinder pressure so that performance stays the same throughout your dive. Cylinder pressure does not influence its operation.
As a result, larger orifices can be used providing more air flow to the diver. This, in turn, makes the regulator breathe easier than a similar though unbalanced design. The greater air flow also makes it easier to supply a second diver who might be breathing from an alternate air source.
Fail-Safe/Free Flow Design:
Fail safe refers to a regulator’s tendency to free-flow because of the use of a downstream valve in the second stage. A downstream valve means that it will tend to open with the flow of air. Therefore, if a problem occurs in the first-stage, the air flow will open the valve allowing air to escape to the second stage. Then, the downstream design of the second-stage valve will also open, causing the regulator to free-flow. This is a vital safety feature.
The primary advantage of the fail-safe design of regulators is that in the event of a malfunction, air is still delivered to the diver. Although the air flow is continuous, it’s a situation the diver can deal with while ascending to the surface. Never continue a dive with a free-flowing regulator even if the air flow is “manageable!”
Environmental Sealing:
An environmental seal operates by not allowing water to directly contact the first-stage piston or diaphragm. It acts instead on a silicone or alcohol based fluid that seal inside a watertight pressure-sensitive barrier and transmits the pressure to the piston or diaphragm.
It prevents salt, sediment and other contaminants from entering the first stage, and so reducing internal corrosion or contaminant build up. It also helps isolate the valve mechanism from freezing temperatures, which is important for cold-water environments, where excessively low temperatures may cause the first stage mechanism to malfunction by freezing.