NOTE: WE DO NOT ENDORSE ANY PRODUCTS WHICH ARE DISPLAYED HERE. THE PICTURES SHOWN ARE FOR REPRESENTATION ONLY.
Scuba Cylinders
Let’s talk about dive equipment theory. Scuba divers breathe compressed air contained in a cylinder. The typical scuba cylinder, or tank, weighs approximately 14kg when empty and holds 2265litres of compressed air at 204bar. This volume of gas would approximately fill a phone booth and weighs about 3.2kg.
Scuba cylinders are made of either steel or aluminium (aluminum alloy).
Steel:
The first cylinders were made from steel and this material remains popular today.
Steel cylinders are hard and therefore resistant to external corrosion. The strength of the material means than steel tanks typically have thinner walls with larger internal volumes for a given external size. Hence it would be fair to say that steel cylinders hold the same air pressure with thinner walls than aluminium tanks.
Steel tanks make your dive equipment a bit heavier, they are negatively buoyant even when empty. The advantage of this would be less weight on the weight belt. The highest capacity cylinders are steel, and coupled with the buoyancy characteristics is why tec divers almost always choose steel for their doubles setups.
The primary drawback is that without proper care, they may rust – an oxidation reaction with iron that yields iron oxide.
Aluminium:
In dive equipment theory we have found out that aluminium is a softer metal than steel, and so more susceptible to external damage. As it isn’t as strong as steel, the walls of aluminium cylinders must be thicker. This makes this type of cylinder larger and heavier out of the water, yet more positively buoyant in the water.
Aluminium does not tolerate overfilling nearly as well as steel does.
Although aluminium corrodes, as does steel, the aluminum oxide adheres to the metal, creating a barrier that inhibits further corrosion. This means that aluminium tanks are far more forgiving in salt water and are less subject to weakening due to corrosion.
Popular cylinders include the 12litre steel and the 11litre aluminum.
Markings:
If you have a look closely at the top of your scuba tank you will notice a lot of tank markings.
Scuba Tanks Cylinder Neck Markings
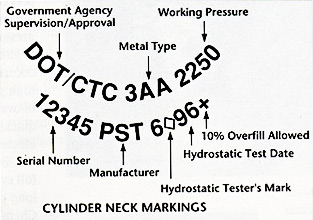
Each of these tank markings in this dive equipment theory have a purpose and are important to determine whether the scuba tank is suitable for you as a diver. The information on the tank should also be referred to when your tank needs re-testing or filling.
Alloy Designation or Metal Type: The 2nd set of characters in the first row denotes the type of metal used in the cylinder. 3AA is the designation for chrome-molybdenum steel. It appears on virtually all steel cylinders in use today. Aluminium cylinders may bear the designation SP6498, E6498 or more typically 3AL.
Working Pressure: The third set of characters in the first row indicate the maximum pressure (in pounds per square inch) to which a cylinder may be filled for normal use. A cylinder should not be filled beyond this point. The single exception occurs with steel cylinders that bear a + (plus) sign (discussed later).
Serial Number: The first set of characters in the second row indicates the cylinders unique serial number. The Manufacturer Identification usually follows the serial number and is the second set of characters in the line.
Hydrostatic Test Date: A cylinders initial hydrostatic test date will usually appear as the last or only item in the last row of information originally stamped on the cylinder. Subsequent test dates may appear anywhere on the cylinder’s neck. The test date numbers represent the month and year in which the cylinder was tested and these numbers are separated by the hydrostatic tester’s initials or a special registered symbol.
Over-Pressurization Designation: The last symbol in the line, a plus (+) symbol, indicates that the tank may be overfilled to 10% of its working pressure. This will appear on steel tanks only and is valid for the first hydrostatic test.
Testing Your Dive Equipment
Hydrostatic Tests
Day to day maintenance of a scuba cylinder is simply rinsing, drying and storing after each use. However, it also needs to be protected from damage, to keep moisture from entering it and to have it inspected and tested regularly.
Many countries require periodic pressure testing to determine the structural integrity of a cylinder. The interval between hydrostatic tests varies from three to seven years (every 5 years in the US, every 4 years in the UK).
The test is called hydrostatic testing as it involves water. The cylinder is filled with water and is placed in a water-filled jacket. It is then pressurized to five-thirds of its working pressure i.e. the tester fills the cylinder to greater than its working pressure (or to a test pressure stamped on the cylinders neck). This pressurizing causes the cylinder to expand and displace water into the jacket. The displaced water rises into a collection tube and a reading is able to determine how much the cylinder expanded.
The pressure is then released allowing the metal to contract and although the high pressure may have caused some permanent expansion, this is acceptable if very slight. If the expansion is too high, the metal is too fatigued to use safely. The cylinder will be stamped with the test date and testers identification symbol if the metal has not expanded beyond a reasonable and safe limit.
Visual Inspection
Most of the diving community require a visual inspection annually. It examines a cylinder internally and externally for any signs of damage or corrosion. Using special lights and mirrors, the cylinder interior is checked for corrosion, stress cracks around the neck and other warning signs.
Rinsing with distilled water and drying with warm air usually removes minor contaminants from the inside of an aluminium cylinder. Minor oxidation in a steel cylinder may be best left in place because the removal process can weaken the cylinder more than the oxidation itself.
If a cylinder has extensive oxidation or deep pitting (oxidation creates a gouge in the metal), it will require sandblasting or tumbling. These methods remove a portion of the cylinder along with the corrosion, so the cylinder will subsequently require pressure testing.
You should test a cylinder ahead of schedule if:
- Loose material can heard rolling around inside.
- Red or greenish material is accumulating on the divers regulator inlet filter.
- The cylinder is filled beyond its working pressure (more than 10%)
- The cylinder has suffered possible impact damage (which requires pressure testing).
- It hasn’t been used in over two years.
If a cylinder is exposed to extreme heat in excess of 82 degrees. This can alter the molecular structure of the metal. This will make it more brittle and less able to withstand constant expansion and contraction. The cylinder with lose its flexibility and rupture when filled. Hence if a tank is exposed to this temperature or above, it will require hydrostatic testing.
Valves
K-Valve: The outside of a valve consists of a simple on/off assembly with a hand turn wheel (knob). You open or close the valve to control the flow of air/gas to or from the cylinder.
J-Valve: Some older cylinder valves may have a reserve mechanism, but these have faded from use. The J-valve got its name from being item number J in one of the first scuba equipment manufacturer catalogues. (The standard non-reserve yoke valve at the time was item K, and is often still referred to as a K-valve) The J-valve predates the submersible pressure gauge.
The J-valve is a spring-loaded mechanism, and was designed as a means to warn the diver has run low on air.
How to learn dive equipment theory
The way that the J valve works is at the beginning of the dive the reserve valve is closed but it is on a spring set to about 20 to 35 bar, so as long as there is more that 35 bar in the tank the spring is pushed back and air flows. When the tank pressure drops below the spring threshold pressure- the spring has more power than the air pressure and it closes. To release the pressure, the diver would pull on a lever (usually pulling the lever to the “down” position) to release the last 35 bar by opening the reserve valve to finish the dive before the reserve was consumed.
On occasion, divers would inadvertently trigger the mechanism while donning gear or performing a movement underwater and, not realizing that the reserve had already been accessed, could find themselves out of air at depth with no warning whatsoever.
When filling a cylinder equipped with a J-valve, the reserve lever must be in the “down” position.
Yoke System: Cylinder valves use either the yoke system or the DIN system. With the yolk system, the regulator fits down over the valve. It is basically an oval metal loop with a screw opposite the regulator that clamps it to the tank valve.
DIN: Deutsche Industrie Norm. With the DIN system the sealing o-ring mounts (is on) the regulator, which screws into the DIN system. Remember: DIN screws IN!
Advantages of using the DIN system over the yoke system include:
A better seal between the cylinder and regulator valves because the O-ring is actually trapped between the two valves.
The cylinder valve and regulator are secured by threads, and so the connection is much stronger than the yoke screw assembly.
The O-ring is enclosed deep within the cylinder valve and is more stable, and enables the use of much higher air pressures.
Burst Disks
Burst disks are required by law in many countries. All cylinders have a maximum working pressure beyond which they should not be filled. To reduce the possibility of over pressurizing a cylinder, a burst disk is installed in the cylinders valve.
A burst disk is a thin copper disk held in place by a gasket and vented plug. If the cylinder pressure rises to approximately 140% of the working pressure, the disk ruptures to allow the air to escape through the vented plug.
Not only do burst disks protect against damage that may occur from overfilling, but also from overheating. If a cylinder is at its working pressure in room temperature, and is then placed in a hotter environment (the boot/trunk of a car), the cylinder will then rise above its working pressure. The burst disk will rupture before the pressure can get high enough for the cylinder to explode.
These can weaken over time and need to be replaced regularly by a qualified equipment technician. During the continual filling and emptying of a cylinder, the disk is constantly stressed and the metal weakens. This means that the disk could blow at a pressure far lower than its rated pressure.
Newer burst disks are designed allowing the air to escape in multiple directions. Older disk plugs allow the escaping air to vent directly out (perpendicular to the cylinder valve), which can result in the cylinder spinning, sometimes out of control.
Depth Gauges:
There are several different types of depth gauges including capillary, open bourdon tube, oil-filled, diaphragm and digital.
In dive equipment theory a capillary depth gauge works by using Boyle’s Law (Boyle’s law describes the inversely proportional relationship between the absolute pressure and volume of a gas, if the temperature is kept constant within a closed system). It is a small diameter, clear, empty plastic tube wrapped around a circular dial. It is open at one end to allow water to enter and closed at the other. As a diver descends, the tube fills with water as the air compress which moves the dial.
In accordance with Boyle’s Law, the internal air space will fill with water in a predictable manner — half the original volume at 10 meters, one third at 20m, one fourth at 30m, etc. By marking off where the water column will be at various depths, a crude but highly accurate gauge can be constructed with no moving parts.
In practice, however, capillary gauges are plagued by problems such as difficulty in seeing the rising water column, increasingly small increments of depths beyond 20m, and air bubbles getting into the tube, making it difficult to read accurately deeper than 10m. For these reasons capillary gauges are rarely used as the sole means of determining a diver’s depth. They are most commonly used as backup devices in shallow water. They are reliable and inexpensive.
It is important to note that the accuracy of capillary gauges becomes an issue when diving at altitude. The capillary gauge will read deeper than the actual depth. A diver at an altitude of 300 meters using a capillary depth gauge indicates a depth of 14 meters for example. However, if the linear distance was measured to the surface, the diver would actually be less than 14 meters below the surface. (see objective 3.14 of the Diving Knowledge Workbook). This is because a closed air space will fill with water in accordance to the relative atmospheres it is exposed to. In essence, it will show a relationship of atmospheres rather than indicate an actual ambient pressure and is why diving at altitude requires special procedures and training.
An open bourdon tube is among the most common pressure-sensing mechanisms. It contains a spiral shaped tube, usually made from copper. Water enters the tub end and when the pressure inside the tube becomes greater than the ambient pressure, the tube tends to straighten. The tube in turn is connected to a gauge needle, which moves with the increasing or decreasing pressure. At altitude, it will read shallower than the actual depth.
The oil-filled gauge also uses a bourdon tube design but here using a sealed tube in an oil-filled housing. The increasing or decreasing pressure is transmitted though the oil and causes the tube to coil more tightly/or loosen. Again this in turn moves the depth gauge needle.
Diaphragm gauges are not as common as others. They function by connecting a flexible diaphragm to a series of levers and gears that move the display needle.
A digital gauge is an electronic gauge that reads depth via a traducer. It will vary the electricity it transmits depending on the pressure exerted on it. It goes on to provide a digital display. The digital gauge offers the highest degree of accuracy.
PRESSURE GAUGES work on the same principle as bourdon tube gauges. The high pressure from the cylinder enters a c-shaped or spiral tube and causes it to straighten somewhat with pressure change, which results in the SPG needle reading the pressure.
By carrying gauges in a wrist mounted fashion, a diver is more streamlined, especially in overhead environments. The console combines several instruments into one package on the SPG or may integrate several instruments into one such as a pressure integrated dive computer. This speeds up dive preparation and doesn’t involve strapping on dive gauges.