NOTE: WE DO NOT ENDORSE ANY PRODUCTS WHICH ARE DISPLAYED HERE. THE PICTURES SHOWN ARE FOR REPRESENTATION ONLY.
Like the diver’s beating heart that moves air from the lungs to the rest of the body, the scuba regulator’s first stage provides the critical connection between divers and the air in our cylinder, allowing us to work and play underwater.
The regulator first stage’s main function is to reduce the high tank pressure to an intermediate pressure that can be utilized by the second stage and provide air on demand to the diver. Modern regulator first stages are precision-made and designed to work under demanding conditions wherever divers care to explore. ( From 200 bar pressure to 12-15 bar pressure)
We’ll be examining both piston and diaphragm first stages, and their differences and similarities to help you understand how this vital piece of equipment allows us to breath while enjoying the ocean’s depths.
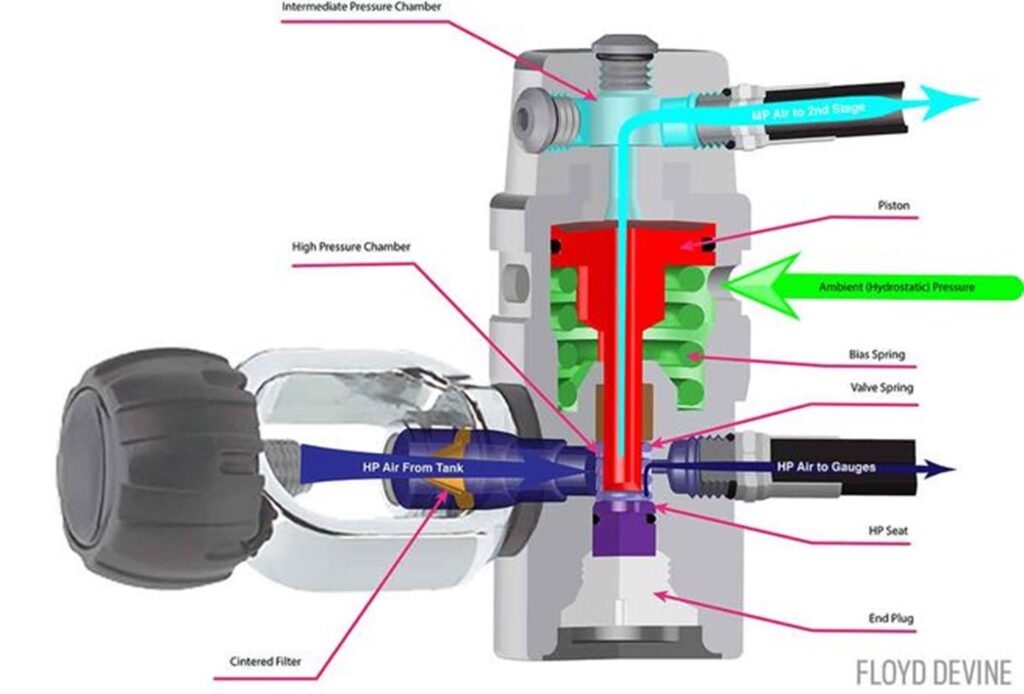
Piston First Stage
1. The Parts
Both piston and diaphragm regulators have either a DIN or yoke style fitting to connect them to the scuba cylinder; an inlet filter to prevent contaminants from entering the regulator; a regulator body incorporating intermediate- and high-pressure chambers; a bias spring; medium-pressure fittings for second stages, inflator assemblies, and accessories; and high-pressure fittings for gauges and transmitters. Piston regulators have a piston-style valve assembly with a high-pressure seat separating the first stage’s high- and intermediate-pressure chambers, while diaphragm regulators have a diaphragm, lifter-poppet valve assembly and high-pressure seat performing the same function.
2. How It Works
As you inhale on the regulator’s second stage, pressure in the first stage’s intermediate chamber is reduced. The force of the bias spring and the ambient water (hydrostatic) pressure push inward on either the diaphragm or the base of the piston head, raising the valve and creating an opening between the intermediate- and high-pressure chambers. Air flows from the high-pressure chamber into the intermediate-pressure chamber and down to the regulator second stage via the connecting hose. When the diver stops inhaling, pressure inside the intermediate chamber increases until it is greater than that of the bias spring and hydrostatic pressure and the valve closes.
The first stage is designed to provide air at ambient pressure, so it must adjust for the changes in pressure as depth changes. To do this, a method is needed for the valve assembly to “sense” the ambient pressure changes and adjust accordingly. Piston regulators have the bias spring, the underside of the piston and a portion of the piston shaft exposed to the water to provide the hydrostatic pressure necessary for operation. Diaphragm regulators have one side of the diaphragm and the bias spring in contact with water to provide hydrostatic pressure, but the rest of the components are sealed off from the environment on the other side of the diaphragm. In both cases, the amount of pressure required to open and close the valve assemblies varies with the ambient water pressure on the exposed surfaces.
3. Balanced vs. Unbalanced
A balanced first stage, whether piston or diaphragm, is designed so that tank pressure does not impact the operation of the valve. This ensures consistent breathing effort independent of depth or tank pressure. Currently, all diaphragm regulators in production are balanced. In diaphragm systems, balancing is accomplished by routing intermediate-pressure air to both sides of the complete valve assembly and passing the valve stem through both the high-pressure and intermediate-pressure chambers. In balanced piston first stages, the incoming high-pressure air does not directly act on the piston-valve, which also passes through the intermediate and high-pressure chambers. Unbalanced regulators have tank pressure acting directly on the high-pressure seat, and incoming high-pressure air will act to close the valve as intermediate pressure rises. This works fine while tank pressures are high and can result in heavier breathing resistance when at higher ambient air pressure (deeper water) or when tank pressure is low. The unbalanced piston will still provide adequate air supply in these cases, but it will require more effort by the diver to breath.
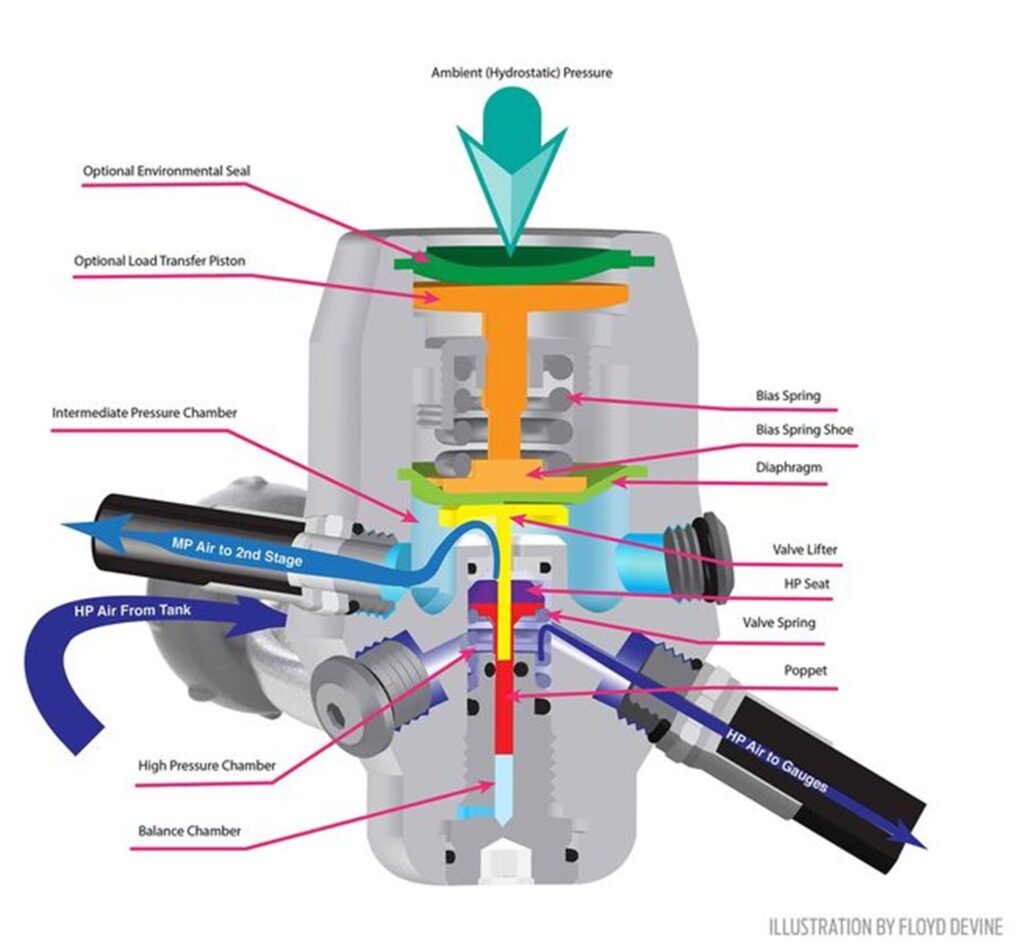
Diaphragm First Stage
4. Piston vs. Diaphragm
Now to the eternal debate over which is best: a balanced piston or diaphragm first stage. It boils down to a matter of personal preference and both designs work well at providing breathable air to their users. There are some distinguishing characteristics, however, that may aid in deciding which may be best for you.
• The nature of a diaphragm first stage’s design means that it is environmentally sealed.
• There is less chance of components being affected by ice particles in cold water, or by silt, sediment, or other contaminants in turbid waters.
• Diaphragm regulators tend to be complex with more parts than a piston regulator and have a smaller diameter valve, meaning lower overall volume of air to the second stage.
• Piston regulators are of simpler design and the size of the piston stem allows for a larger volume of air to be supplied to the second stage, making them popular for their ease of breathing effort.
• Piston regulators have more components exposed to the environment, making them more susceptible to contaminants affecting performance, icing in cold water and resulting free flow from a stuck piston.
• Piston regulators may require more maintenance of exposed parts due to contamination.
5. Additional Features
Regulator first stages are closed systems and are not designed with user-adjustable features, but there may be enhancements incorporated by the manufacturer. Both types of regulators may incorporate environmental protection, to include a second diaphragm to protect the bias spring of a diaphragm first stage, or by filling the exposed section of a piston regulator with a viscous fluid and sealing it off with a flexible ring. Some regulators incorporate automatic devices to close the high-pressure inlet and prevent contaminants or water from entering the first stage when the regulator is not connected to a tank. Some regulators may incorporate a special medium-pressure port with greater airflow specifically designed for high performance second stages.
How a Scuba Diving Regulator’s Second Stage Works
Have you ever wondered how regulators make it possible for scuba divers to breathe pressurized air underwater? Well, here’s an illustrated explanation on half the equation: how a scuba diving regulator’s second stage works.
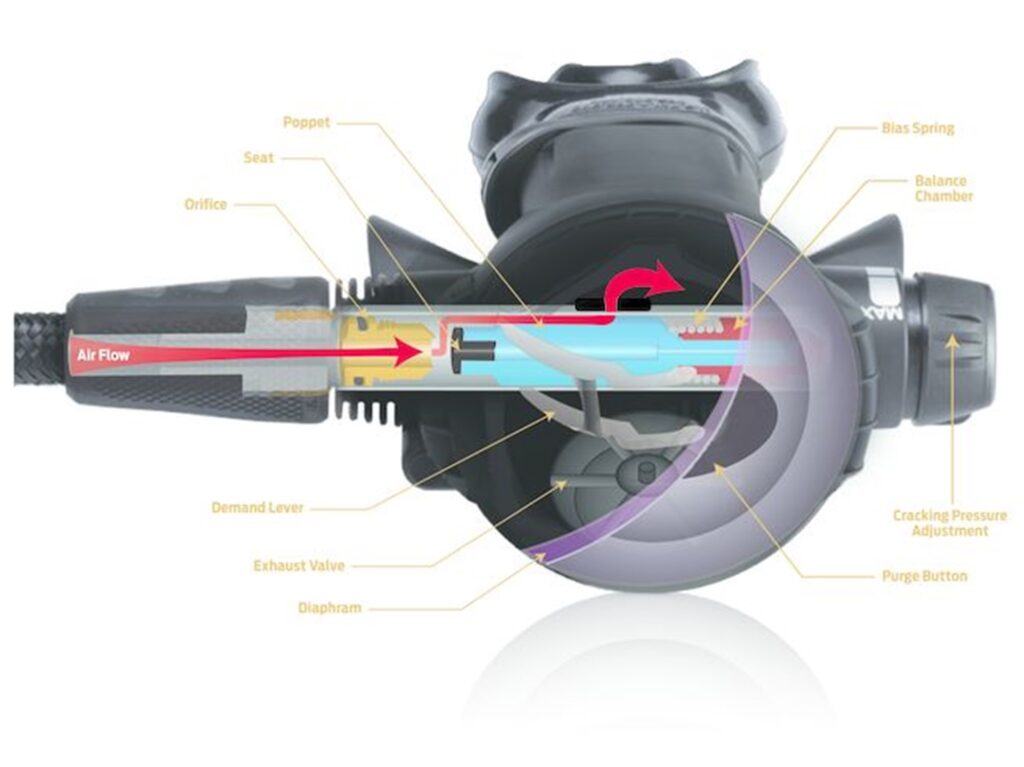
The second stage of a scuba diving regulator
We’ve come a long way since the early 1940s when Jacques Cousteau and Emile Gagnan, made by Aqualung, underwater regulators, modified from Gagnan’s demand regulator that fed cooking gas to a car’s carburetor in the exact amount needed. Remarkably, today’s regulators rely on the same design principles used by Cousteau and Gagnan. You cannot breathe directly out of your tank because the high pressure would damage your lungs. Just like the Aqua-Lung, today’s second stages take pressurized air from the first stage and provide it to a diver at ambient pressure, allowing him or her to breathe normally underwater. Through the use of precision manufacturing, high tech materials and intensive testing, modern regulator design is efficient and reliable, and with proper maintenance and care, modern second stages will provide years of dependable operation.
1. The Parts: Mouthpiece, housing, cover incorporating a purge valve, flexible silicone diaphragm to separate the external water from the housing, demand valve assembly, demand lever and exhaust valve.
2. How It Works: Air from the first stage enters the second stage housing through an inlet fitting. At the inlet, an orifice with a circular “knife edge” provides a sealing surface for the main valve assembly. This assembly consists of a poppet with a hard-rubber seat at one end, a bias spring and the valve body. The bias spring applies pressure on the poppet, pressing the seat against the edge of the orifice and creating an airtight seal. The demand lever is attached to the valve body and compresses the bias spring to pull the poppet away from the orifice, allowing air to flow into the valve.
As you inhale, pressure in the second stage is reduced and the diaphragm is pushed inward by the surrounding water pressure. The diaphragm then pushes on the demand lever, opening the valve. With the valve open, air then enters the second stage through an opening in the valve housing until it equalizes with the surrounding water pressure, making it possible for a diver to breathe air at ambient pressure. When the diver stops inhaling, pressure inside the second stage increases, causing the diaphragm to relax and release the demand lever, closing the valve.
This reduces the pressure from 12-15 bar pressure to ambient pressure
As the diver exhales, air is expelled through the exhaust valves. The design of the second stage keeps ambient pressure in the housing at the same pressure as the surrounding water, ensuring that the reg enables consistent breathing effort regardless of conditions and depth.
3. Additional Features: Many regulators have cracking pressure adjustment knobs, Venturi adjustment controls, and a balancing chamber in the demand valve. In a balanced second stage, a balancing chamber is added to the end of a modified poppet with a drilled-out center chamber and a hollowed-out seat. When a balanced second stage valve is closed, air travels through the opening in the seat and poppet into the balance chamber, pushing the poppet back against the orifice. This means a lighter bias spring can be used and less effort is required to open the valve. A cracking pressure adjustment manually changes the tension on the bias spring to increase or decrease the amount of effort required to open the valve, and the Venturi adjustment moves a rotating vane to direct air flow toward or away from the diver’s mouth. Both features potentially reduce breathing effort and aid in managing free flows.
How To Care For Your Scuba Regulator
The regulator is a link to the underwater for scuba divers, and a piece of equipment that needs to be in tip-top shape and monitored for performance constantly. Make sure you take care of your reg by properly prepping it for a dive and cleaning it afterward. Here are a few maintenance tips for keeping your regulator in tip-top shape for as long as possible.
REG CARE — BEFORE YOU DIVE
• Carefully check the hoses on your reg for signs of wear or damage
• Check the fittings and filter for corrosion
• Check the venturi and breathing adjustments to make sure they operate smoothly
• Inspect the mouthpiece for damage or wear, and make sure it’s securely fastened
• Check for leaks; with the dust cap still on, or the reg connected to a tank with the valve still closed, try to inhale through the mouthpiece; if you can draw air in, there’s a leak somewhere, most likely the exhaust diaphragm
• Finally, connect your reg to a tank and open the valve fully, then exhale and take several deep breaths while watching the pressure gauge; the pressure shouldn’t drop; if it does, it’s a sign of a restriction or other problem that requires service
REG CARE — AFTER YOU DIVE
• If possible, soak your reg while connected to a tank with the valve open – that way, no water can get into the first stage where it can cause corrosion
• If you don’t have a tank handy, keep the dust cap securely in place; the important thing is to keep water out of the first stage
• Soak your reg thoroughly in clean fresh water to remove any salt, sand or other debris
• While it’s soaking, slide back hose protectors to expose the fittings
• Operate the breathing adjustment and Venturi switch and let water run through the second stage
• Don’t press the purge while soaking if the reg isn’t connected to a tank, because that can let water into the first stage
• Finally, dry your reg out of the sun before replacing the hose protectors and storing it for your next dive